How to minimise the cost of transporting your new modular home
When you're building a modular home, one of the most critical costs to keep in mind when planning your budget is the cost of transporting the house from the factory to your block of land.
There are a few factors to keep in mind when designing your home which are especially important if you’re a long way away from the factory. This will help you minimise transport costs while still maximising your floor space.
Westbuilt has a team of modular home designers and builders on hand who specialise in creating high-quality, cost-effective modular homes. A part of our process is helping our clients understand the ins and outs of transporting modular homes in order to guarantee a smooth transition from factory to build site to eventual move-in date.
We recommend you take the time to read through this short article. It outlines the main causes of overly expensive transport costs in modular homes and how to minimise them.
Key cost factors
Five critical factors determine the cost of transporting a modular home to your site. These are;
- Distance – how far away you are from the factory
- Width – the overall width of the modules.
- Height – the height of the module
- Truck Loads – the number of modules needing transport
- Site access - difficult to reach blocks of land will drive up costs
Distance from factory
The number of kilometres between your site and the factory will determine how much your home is going to cost to transport.
While we don't have much control over this, we do strive to do everything possible to ensure that the cost of transport is as low as possible.
This is especially relevant when considering the module width of your home. For instance, moving one massive 5.5m module using a single truck 20km from the factory may only add a few thousand pounds more to the overall house, while the cost of transporting the same module using a single truck 400km may be 10 or 20 times more than the original price.
As we explain next, it may be cheaper to split a wide module into 2 narrow ones.
Module width
Let's consider some of the road restrictions and regulations for wide (and high) loads in QLD & NSW.
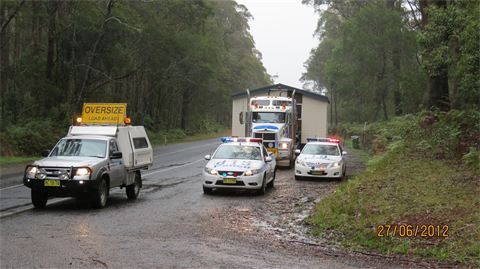
- Up to 3.5m = No pilot vehicles required, the most cost-effective option.
- 3.5m to 4.5m = Single pilot vehicle to accompany load.
- 4.5m to 5.5m = Three pilot vehicles to accompany load plus police escorts on specific roads and highways near major population centres.
- 5.5m wide and over = Dependant on the route – not advisable due to lack of cost-effectiveness. There is a lot less cost involved in sending two 4.0m modules than one 5.6m module.
Because wider modules require more escorts, we aim to minimise the width of the modules we design in order to minimise the number of escorts required during transport and balance that with the number of modules needed to construct the house.
Module height
Another constraint imposed on the transport of modular buildings is the height of the load on the road. Most major highways have a height restriction of 5.0m.
If the modules for your home end up over 5.0m, additional high load pilot vehicles and approvals from utility companies will be required.
Module length
Modular lengths are limited by the truck and trailer combination, along with the practicality of manoeuvring the module. At Westbuilt we recommend our clients keep the module length below 18 meters to allow easy, cost-effective transportation.
Truck loads
Larger homes may require more modules to accommodate the various rooms and living spaces and thus the number of truck loads required is higher. In order to reduce transport costs, you can opt to maximise the use of space by incorporating multi-functional rooms and utilizing open floor plans.
Site access
Other significant impacts on the cost of transport are fixed obstacles such as low clearance bridges, load limits on bridges or low-hanging wires. Further considerations are the slope of your site, ease of access and wet ground.
The most cost-effective module size for transport
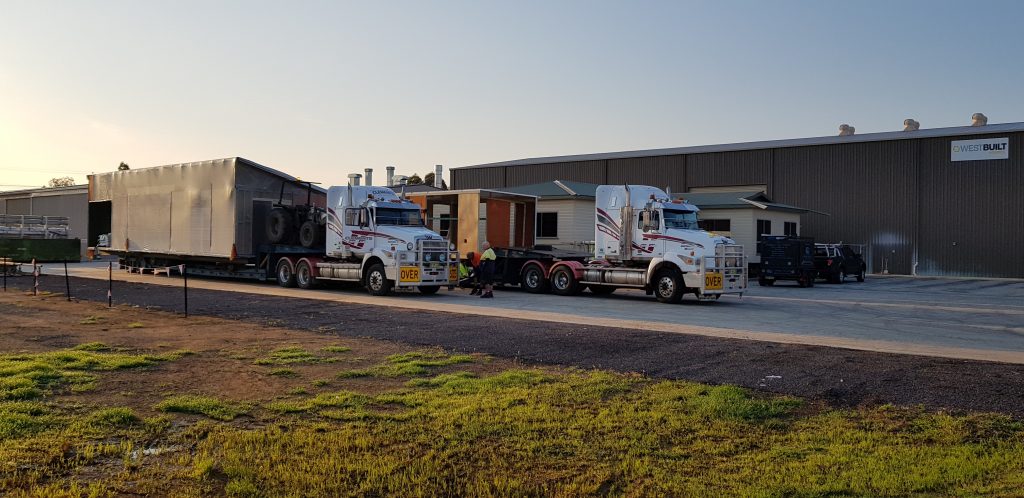
We’ve found that the most cost-effective module size is a 16.5m long x 4.0m module. However, this really does depend on the actual size of your home and your specific design.
In order to minimise the cost of transporting your modular home, while not decreasing floor space, be sure to consider the following points;
- Reduce the number of pilots needed. Look at designing your home with a maximum module width of 4.4m. This means that you are limiting the transportation to just one pilot vehicle per truckload because let’s face it – any more than one pilot vehicle is really a bit of a waste of time and money.
- Balance it with the total number of modules. Following on from reducing the module width, consider ways of ensuring your home is designed with a minimal amount of modules as practically possible.
- Consider the Westbuilt fold down roof system. This innovative method of folding the roof of the home for transport is an excellent way of minimising transport costs caused by over-height loads. Contact one of the team for more info on this system.
Conclusion
We hope this article will give you some insight into what is involved in the cost of transporting your new modular home.
One of the benefits of modular homes is their speed of construction, quality of build and controlled cost. And by considering, early in the planning process, the cost of transport can go a long way to making your new modular home cost effective.
Lastly, we would like to point out that we don’t expect our clients to understand the finer points of designing modular homes. That is what our team specialises in, and we’re here to help you. One of the considerations we will discuss with you early in the process is how to tweak your design to minimise transport costs.
To find out if you can get a modular home on your site check out this article here.